As part of the RICS construction technology one needs to know a number of basic construction technology. In this series of blog posts we’ll be covering the substructures.
Buildings are separated into two parts: the part generally below the ground floor and which extends down into the ground, and the part above the ground floor. This blog post covers the substructure, from ground conditions to building construction from the foundation below.
The classification of ground conditions
When we think of ground conditions, they’re usually classified as either topsoil or subsoil. Organic matter is a big part of topsoil, which also has a high concentration of insects and worms. Vegetation grows in topsoil, and that’s what people usually refer to when they say “topsoil”.
What is Topsoil and how do you deal with it
Below the layer of topsoil there is a thin layer where both topsoil and subsoil mix. It’s considered “topsoil” for our purposes in building construction. This transitional area marks the meeting between the two types of soil.
The layer beneath the topsoil is without any organic constituents, although this layer might be home to living creatures that burrow below the soil.
The layer beneath the topsoil is without any organic constituents, although this layer might be home to living creatures that burrow below the soil.
Building Regulations require that soil beneath the building be completely excavated. The consequences of not doing so vary depending on a range of factors, but are mainly based on three reasons:
The thickness of topsoil in the UK
The thickness of topsoil in the UK
With any building, the thickness of the topsoil will always affect the cost. Remember, you have to remove thicknesses, which makes things more expensive. Around the UK, there’s a general thickness of 200mm200mm at ground level where farmers have cultivated it and a depth of 100-150mm100-150mm
Untouched areas with good vegetable growth are common, but there are exceptions where soil health is prevalent, or large areas with peat or little growing on them.
Demolition sites and dumping sites can result in depressions with less than ideal topsoil conditions.
We won’t discuss extreme conditions, but will focus on simple topsoils over stable subsoils.
Many drawn presentations are designed without considering the site or situation they will be used for.
The standard thickness of topsoil is typically 150 mm150 mm.
When building a structure, it’s common to remove topsoil from the immediate area using excavators (360).
Topsoil is often needed for garden ground around the building, so it must be preserved.
There is a special way of preserving and storing topsoil on site, detailed in the British standard (3882:2015).
Spoil and taking it offsite
Spoil and taking it offsite
Any excavated material is called spoil and can be disposed of offsite or placed onsite.
Any excavated material is called spoil and can be disposed of offsite or placed onsite.
Topsoil can be removed from the site as long as it’s disposed of, stored correctly.
Topsoil can be removed from the site as long as it’s disposed of, stored correctly.
Topsoil should be immediately spread around the site being worked on when performing this process. Bringing the surface to a desired level, this step is typically called “spreading and levelling”.
Topsoil should be immediately spread around the site being worked on when performing this process. Bringing the surface to a desired level, this step is typically called “spreading and levelling”.
The spoil heaps for topsoil shouldn’t be higher than two and a half metres. Storage in higher heaps can cause a problem for the soil in the long term and kill the bio-organisms living in there for the plant.
The spoil heaps for topsoil shouldn’t be higher than two and a half metres. Storage in higher heaps can cause a problem for the soil in the long term and kill the bio-organisms living in there for the plant.
Three types of subsoil
Three types of subsoil
There are three types of subsoils:
- These soils are able to carry the weight of a low-rise building without any special construction techniques or precautions.
- Those who are able to manage the structural load of a much larger building with efficient foundation techniques.
- Unique circumstances require special techniques or precautions for even the most basic of structures.
Soils are classified into different types, with subsoil being one of them. It’s a layer of soil that transitions gradually from the topsoil and generally occupies a layer 50-75 mm thick.
Subsoil is not a fixed layer and can vary in thickness and density. It’s essential to consider the load-bearing capacity when placing foundations.
Load-bearing capacity refers to the force that acts on a unit area, causing a foundation to fail. A margin of safety is necessary to determine the safe load-bearing capacity.
Regardless of the thickness or density of the soil, it is essential to consider loadbearing capacity when placing a foundation.
To determine the loadbearing capacity of a foundation when constructing walls on a building site, classify the subsoil into various types.
Designs have been greatly improved since the early 20th century, and new books generally contain an approximation of this capacity in kilonewtons (kN) or newtons (N).
In order to determine the loadbearing capacity of a foundation when constructing walls on a building site, the general approach is to classify the subsoil into various types.
Designs have been greatly improved since the early 20th century, and new books generally contain an approximation of this capacity in kilonewtons (kN) or newtons (N).
This capacity is adequate for common work that includes foundations as long as it’s adjusted to safe loadbearing capacity.
Thinner soils or layers with lower capacities may require professional intervention from soil mechanics specialists.
These specialists are available to inspect the subsoil at your building site and analyze its strengths and weaknesses by testing for loadbearing capabilities.
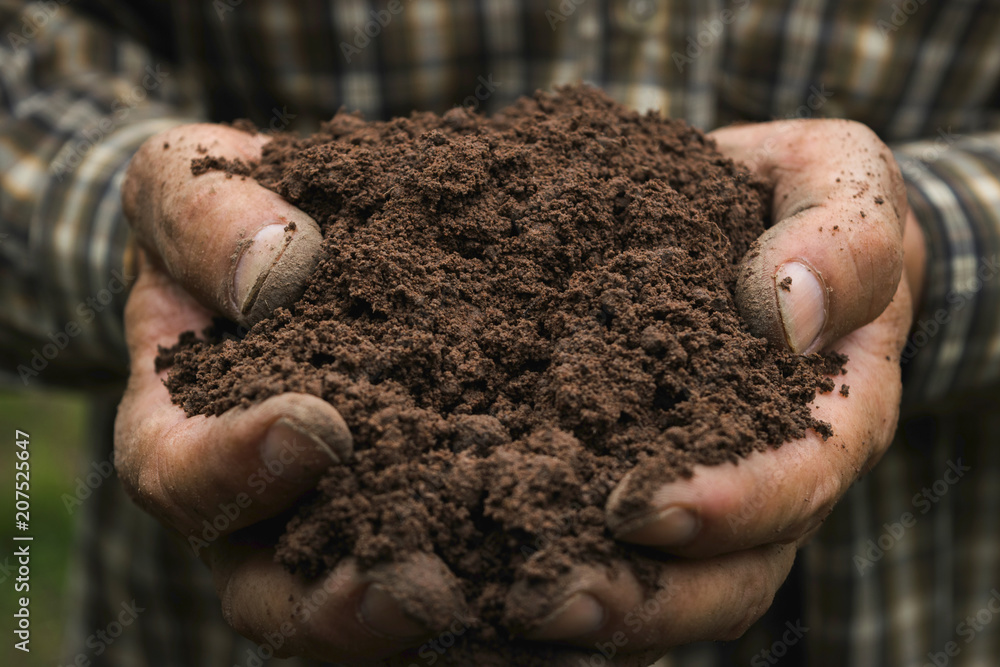
soil
The Categorization of Subsoils and Their Loadbearing Capacity
The Categorization of Subsoils and Their Loadbearing Capacity
The Building Regulations generally have a lot to say about loadbearing capacities. In this case, the Regulation takes the form of reference tables for foundations that identify a range of widths for strip foundations in various mixtures.
Soil type can be determined on the basis of whether it is gravel, sand, silty sand, clayey sand, silt or rock. The condition of each soil type can be assessed with regard to its compactness, firmness and softness.
Only rock foundation strips are allowed to be as wide as the wall itself. Other foundation services must meet specific minimum widths depending on the subsoil and its condition.
Here are some tables that have been used in building research to develop tables for optimum foundation widths. Although they vary slightly, they are all based on Building Research Station Digests 64 and 67 published in the 1970s.
For example, one table quoted in some Regulations gives a width of 400 with a wall load of 40 kN/m^2. If you take the time now, you will see that this equals 100 kN/m^2. This is despite the fact that maximum loadbearing capacity is up to 600 or even 1000 kN/m^2 in many textbooks!
Approved by rule of thumb cited above, calculated safe bearing capacities would be 150 and 300 kN/m^2 respectively, which indicates that the figures quoted in the Regulations for foundation widths and safe bearing capacities have a much higher margin of safety.
Foundations
Now that we’ve looked at the properties of different soil types, it’s time to look at foundations. There are a wide variety of loadbearing characteristics in the soil tables mentioned earlier, and you’ll need a few techniques to build on different ground conditions.
First, you should know that most foundations are made by pouring wet concrete into holes drilled in the ground. The shape can be made as simple or complicated as you require, and everything in between.
You’re only concerned with straight pieces of concrete cast into the ground that present a flat surface where walls can be built upon. Concrete is discussed more thoroughly in Appendix D, which should be read if this chapter gets too technical for you.
Approved by rule of thumb cited above, calculated safe bearing capacities would be 150 and 300 kN/m^2 respectively, which indicates that the figures quoted in the Regulations for foundation widths and safe bearing capacities have a much higher margin of safety.
For example, one table quoted in some Regulations gives a width of 400 with a wall load of 40 kN/m^2. If you take the time now, you’ll see that this equals 100 kN/m^2.
This is despite the fact that maximum loadbearing capacity is up to 600 or even 1000 kN/m^2 in many textbooks!
The foundation of a building with a simple rock base is rock solid. No elaborate foundation is needed.
Strip foundations are often used for medium-sized buildings that stand on stable ground and can withstand natural earth movements.
In contrast, deep strip foundations are used for larger buildings that need more support against forces that could move the base of the building away from its walls.
In strip foundations, a wide trench is dug with walls built off of the layer of concrete.
Deep strip foundations involve a narrow trench, not much wider than the wall, dug and then filled up with concrete almost to ground level.
The other extreme would be soft ground overlying a firm strata with good loadbearing characteristics.
When it comes to building a structure, an engineer must be aware of the type of ground (e.g. crystalline, sedimentary) that is supporting the building and choose appropriate construction methods and materials accordingly.
In cases where there are large piles present in solid soil strata beneath the building site, they can be driven until they reach the bearing layer.
Once this has occurred, beams can be cast into these piles to form the foundation for desired buildings.
However, if there are high concentrations of waves or slides present beneath the site, this process would most likely prove ineffective.
For this case we could use the raft type of foundation instead — which would involve placing a thin layer of concrete over areas that requires support for the building and then hoisting them up higher so that water filters through and carries away any rough spots below it.
If this is not a feasible option or something you feel like doing yourself, then piling might be another great alternative.
This involves driving long columns of materials – usually concrete – into the earth to ensure a stable foundation can be built on top of it afterwards; just make sure to keep in mind that you need to know what type of ground (e.g. crystalline, sedimentary) you’re working with before building the foundation.
Soil shrinkage and swelling can cause buildings to be displaced. Plants absorb a substantial amount of moisture from the ground, which is released into the atmosphere through transpiration. Trees are significant water users, with species like poplars and willows using more water than most. This allows them to extract moisture from clay during drought conditions, causing clay to shrink. To avoid issues, trees should be kept away from buildings, especially when dealing with shrinkable clay.
Moist subsoil can lead to building instability due to freezing. This occurs when the subsoil remains moist and then freezes, causing the soil to expand and exert pressure on the surrounding soil and structures.
Conclusion
Understanding the two main types of soil and the three types of subsoil is crucial for making informed decisions about construction and soil management. If you have any questions or concerns, please leave a comment below.